
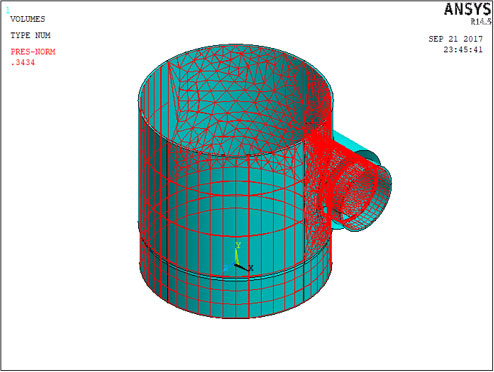

The process design methodology using process integration and hazard modeling tools by integrating the energy, economic, and safety approaches at the initial design stages itself is useful to design efficient new plants and to increase the profitability and the safety of the existing methyl chloride production plants. The API 2000 calculation program will solve for the volumetric capacities of vents and gas valves to properly gas blanket a. The results of this research can be implemented in process engineering design. A quantitative risk assessment was performed by hazard modeling studies using the ALOHA modeling tool for methyl chloride leak from the storage tank. The location of the pressure safety valves, orifice sizes are calculated for the entire process plant and the storage tank. Product cost is reduced by 2.78 USD per ton, Greenhouse gas emissions reduced by 26%, and carbon tax by 26.34%. The payback period is reported as 0.63 years. Energy analysis improved the total utilities saving potential up to 36% by adding two new heat exchangers to the existing design. Using the simulation model results an attempt has been made to improve the methyl chloride production process plant's efficiency in the aspects of energy, economy, safety, and sustainability using process integration. In this research, a model simulating the methyl chloride production process through hydrochlorination of methanol is investigated. Based on its industrial importance and safety issues, this research focused on improving efficiency and process safety. Because of its toxic, flammable, and explosive nature, safety is also equally important. Methyl chloride is the starting material for various chemicals of industrial importance. Search for jobs related to Api 2000 venting calculation excel or hire on the worlds largest freelancing marketplace with 20m+ jobs.
